Indonesian manufacturer extends itsrange of services, with help and expertise from Weckenmann.
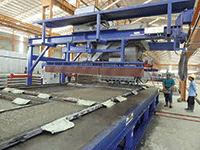
Based inthe Indonesian capital Jakarta, PT. Rekagunatek Persada is a subsidiary of PTIndonesia Pondasi Raya, Indonesia’s leading specialist foundation engineeringcompany. The company decided to set up a plant for the production of precastconcrete parts for housing and building construction to expand its range ofservices in this area.
Afterhaving already been involved in the foundation work of many of the existingbuilding projects and already having produced precast concrete parts for civilengineering in the past, the precast concrete parts to be produced now shouldbe of particularly high architectural and structural quality for high-riseresidential housing. The high demand for these products and services was drivenby the numerous construction projects planned in Greater Jakarta, which were inthe implementation and planning stages.
Aftervisiting several reference plants in Asia and Europe, the company decided tocollaborate with one of the major global plant specialists, WeckenmannAnlagentechnik GmbH & Co. KG., from Germany. Weckenmann convinced theclient with its broad production portfolio engineered and made in Germany.
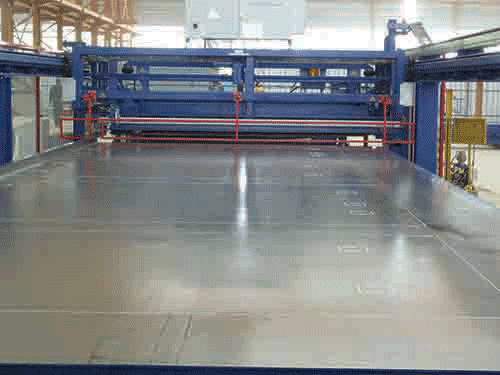
Investment in a central transfer table system
Thedecision to build a central transfer table system was based on the specialrequirements for production flexibility. The investment in the central transfertable system for the production of solid wall panels represents the first stageof the complex production plant at a newly developed production site.
Approximately700 m2 of wall panels can be produced per shift on a total of 22shuttering pallets with a gross production area of 4.3 x 12 metres. The wallpanels are solid partition walls as well as façade elements with partlyarchitecturally structured fair-faced concrete surfaces. The formwork surfacesare precision machined to produce perfectly smooth and level surfaces.
Thedesign of the central transfer table system concept allows different lengths ofstay in the individual workstations, without shuttering pallets with a longerprocessing time impeding the material flow of pallets with a shorter processingtime, unlike in a conventional circulation system. Overall, the system isequipped with 29 working and curing positions. These are all on one work level.
Reinforcementcage production is currently still done offline. The reinforcement cages areproduced using standard mats and placed in the shuttering pallets.
Twentywork positions are provided for curing and surface finishing. The freelyselectable access work positions for the simultaneous curing and surfacefinishing allows the surface to be finished with a helicopter trowellingmachine at the technologically correct curing time of the produced concreteelements, without the pallets having to be moved again during the curing time. Thehelicopter trowelling machine moves over the entire curing range of 20positions.
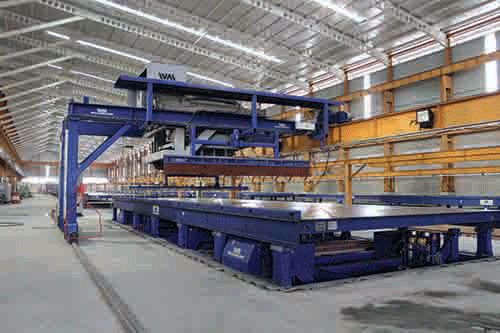
A specialfeature of this concept is the circulation running parallel to the centraltransfer table between the following positions:
-
Pre-stripping.
-
Stripping the end of the shuttering pallet.
-
Stripping.
-
Cleaning and plotting.
As theseprocesses can take place independently of the operation of the central transfertable, the operation of the central transfer table is accelerated withoutrestricting the flexibility of the system.
Shuttering pallets with side rails
Theshuttering pallets are fitted with side rails that are permanently mounted onone-side, but that can be replaced by unscrewing them. The side rails aredesigned to act as a levelling mechanism for the bull float of the concretespreader at the top so that an exact level can be achieved by screeding andsmoothing the elements.
Differentformwork heights are made possible by reusable shuttering rails, and differentformwork contours by magnetically adhering moulding profiles. The load on theshuttering pallets is up to 1,000 kg/m2, which means elements of upto 400 mm thick, can be manufactured.
M series shuttering system in use
Theshuttering profiles as well as the recesses for door and window installationsare produced by the proven M series shuttering system with integrated switchablemagnets. This shuttering system is individually equipped with the requiredprofiles for the formation of the grouting and abutment surfaces as per thecustomer's requirements. Depending on the type of production, telescopicextension profiles are provided to adjust the individual lengths of theshuttering profiles.
Theproduction data is transferred from the CAD system via a DXF data interface. TheWAvision light master computer program is used for the production planning andoptimisation of the pallet loading. The production data is transferred to thecleaning-plotting-oiling machine by means of a USB stick.
Thecleaning-plotting-oiling machine is a multifunction machine which has thefollowing functions:
-
Cleaning the shuttering surfaces.
-
Plotting the production data 1:1 on the formwork table surface.
-
Oiling the pallet by applying forming oil agents to the formwork surface.
As theshuttering pallet passes through this workstation, preparation for the nextproduction run is done quickly and with controlled quality, all in one go.
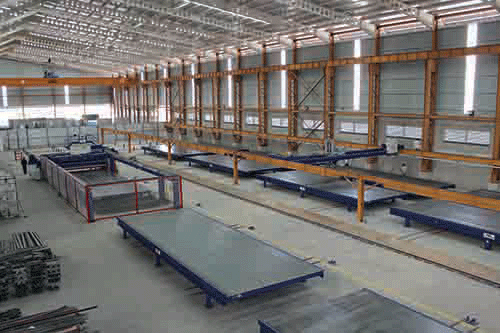
Integrated concrete batching plant
Aconcrete batching plant integrated in the system concept produces freshconcrete. The bucket conveyor spreads the concrete required. This is controlledby a control panel on the concrete spreader.
Using acommunication interface to control the process, the exact amount of concreteneeded is prepared in the concrete batching plant, ensuring a just-in-timeconcrete supply to process the concrete without loss of quality, which is veryimportant in the prevailing temperatures of this tropical climate.
Ahalf-gantry concrete spreader with a transversely slide-able applicationcontainer processes the concrete through specific spreading of the concrete. Theconcrete spreader with spiked roller discharge and eight slides allows thescreeding of the wall panels directly during concreting.
Theconcrete is compacted by means of a combined high-frequency low-frequencyvibrating/shaking station while concreting is taking place. Combining these twoprocedures enables optimum compaction in different floor slabs and concreteconsistencies.
Theoperated plant allows excellent production flexibility due to the material flowdesign of the central transfer table. The shuttering pallets with two loadlevels (500 kg/m2, 1,000 kg/m2) in combination with theflexible shuttering system are equipped for future expansion of the productrange.
The basicautomation of the system enables high-quality production with a manageableinvestment budget. The production layout allows the expansion of productioncapacities. The system concept is designed to be ready to increase productivityeven more by retrofitting a shuttering robot.
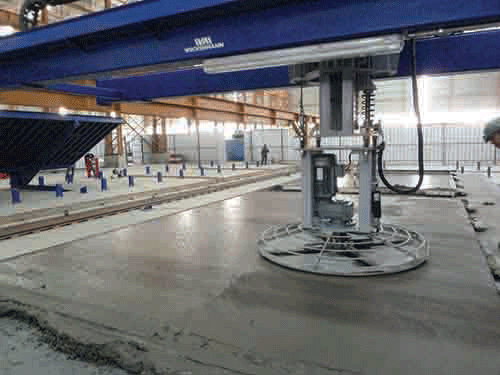