Prefabricated steel construction istransforming India's infrastructure landscape, and Kirby India is at theforefront of this transformation.
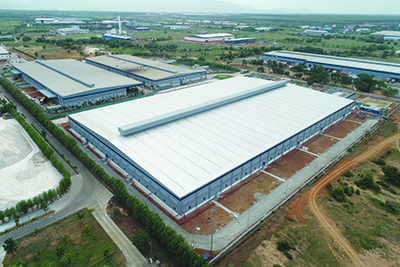
As rapid urbanization andinfrastructure expansion continue, the need for faster, cost-effective, andsustainable building methods has become imperative. Prefabrication, onceconsidered a niche market, is now emerging as a game-changer, redefining how buildingsare designed and constructed. The Indian market is embracing this evolution,supported by technological advancements, government initiatives, and anincreasing focus on environmental sustainability.
In recent years, the prefabricated steelconstruction sector in India has seen exponential growth, largely due toindustrialization and the need for efficient building solutions. Advancedtechnologies, such as Building Information Modelling (BIM) and smart buildingsystems have significantly improved the precision, quality, and efficiency ofprefabricated structures.
Sustainability has also become amajor driving force, as prefabrication minimizes construction waste andpromotes the use of eco-friendly materials, particularly steel. Governmentpolicies, including Make in India, the PLI Scheme, National Logistics Policy, andmajor infrastructure programs like Gati Shakti, Bharatmala, Sagarmala, andSmart Cities, have provided an impetus to the sector, facilitating itswidespread adoption.
[!image3:n![
The Indian prefabricated buildingmarket is poised for further expansion, with reduced construction timelines,cost efficiency, and increased private-sector investment fuelling its growth. Asdevelopers and construction firms prioritize speed, durability, andsustainability, prefabrication is set to play a crucial role in shaping thefuture of India’s built environment.
Several high-tech prefabricatedsolutions have gained prominence in the Indian market, catering to diverseneeds across industries. Kirby India is at the forefront of thistransformation, delivering customized factory buildings, industrial structures,high-rise commercial spaces, data centres, airtight buildings, andgreen-certified structures.
Advanced prefab technologies areenabling streamlined processes, reducing environmental impact, and enhancingstructural durability. A growing number of manufacturers are focusing oncreating prefabricated structures offering precise customization with efficientproject management.
These innovations allow complexarchitectural designs to be executed with minimal waste, ensuring highefficiency and sustainability. Moreover, prefab solutions are aligning withgreen construction practices by incorporating renewable energy systems andenergy-efficient materials, making them a viable option for eco-consciousdevelopers.
With sustainability becoming a corefocus, the demand for energy-efficient buildings is shaping the design andmaterial selection in prefabrication. Modern prefab buildings are incorporatinghigh-performance insulation materials and sandwich panels to enhance thermalperformance.
Smart building technologies,including solar panels on roof sheeting and battery storage systems, are beingintegrated into prefab structures to improve energy efficiency and reduce relianceon traditional power sources. The adoption of passive design strategies isanother key trend, with modular buildings being oriented to maximize naturallight and ventilation.
Off-site manufacturing ensuresminimal material wastage, while strict quality control measures enhance theoverall efficiency of prefab structures. Additionally, regulatory compliancewith standards, such as IGBC, LEED, EDGE, etc., is driving innovation in prefabsolutions, making them an attractive choice for forward-thinking developers.
Prefab construction is poised tobecome a standard practice in India, driven by its cost-effectiveness, speed,and sustainability. It enables 30-50 per cent reduction in build time, makingit ideal for large-scale projects.
With India's urban populationprojected to reach 600 million by 2030, the demand for fast, scalable, andsustainable construction is rising. Prefab solutions can play a crucial role inmass housing and commercial infrastructure.
However, overcoming resistance fromtraditional builders, regulatory hurdles, and logistical challenges isessential. With policy reforms and technological advancements, prefabconstruction is set to become a preferred choice across industries.
Despite these challenges, theoutlook for prefabrication in India remains promising. Government initiativesand policy reforms are expected to streamline regulatory approvals, whileautomation, AI-driven design, and 3D printing will further enhance theefficiency and affordability of prefab construction. As more developersrecognize the benefits of faster project completion, reduced costs, andsustainable construction, prefabrication is likely to gain mainstreamacceptance, particularly in commercial and infrastructure projects.
The construction industry in Indiastands at a pivotal moment, where prefabrication could redefine the waybuildings are conceived and executed. While its widespread adoption inresidential sectors may take time, the future of prefab construction isundoubtedly bright.
By embracing innovation andovercoming regulatory barriers, India can position itself as a leader inadvanced construction methodologies, paving the way for a more sustainable andefficient built environment.