Nitrogen generators are nowconsidered essential equipment in various sectors of the economy. Thesegenerators pave the way for a more productive, sustainable, and competitive futurein manufacturing and other industries, writes Bhushan Bokil.
“On-site generationremedies all these shortcomings. It can be achieved at a fraction of the costincurred when sourcing it from a vendor and leaves a low environmentalfootprint.”
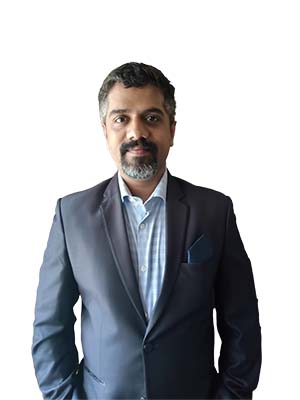
- Bhushan Bokil,
Business Marketing Manager,
Industrial Air,
Atlas Copco.
Nitrogen plays a big rolein various industrial applications. It is often referred to as the fifthutility, alongside water, electricity, gas, and compressed air. This calls fortwo approaches: buying nitrogen from a third-party source (cylinder gas, liquidbulk gas, and on-site cryo production), or on-site generation. It has become agrowing trend in the market to purchase on-site nitrogen generation solutions.
Nitrogen is effectivelyeverywhere. Yet, manufacturers resort to ordering nitrogen, which is mostlystored in big, heavy gas cylinders based on its usage. Alternatively, theyinstall a liquid nitrogen storage tank on the site and get it filled upperiodically with purchased liquid nitrogen.
These are some of the commonways of obtaining nitrogen, but these methods are not always the most idealoption. That is because it puts quite a load on the environment: the logisticson your site requires time from your personnel, there is always a portion ofgas that is wasted, and they come with certain workplace risks. Above all, thetotal cost over a couple of years can add up to a significant amount.
On-site generation remediesall these shortcomings. It can be achieved at a fraction of the cost incurredwhen sourcing it from a vendor and leaves a low environmental footprint.
Companies that neednitrogen on a daily basis, stand to gain a lot from on-site generation. Thebenefits include:
1) Lowest total cost perunit of nitrogen produced – improved bottom line.
2) No long-term and complexthird-party supply contracts – stable and predictable costs.
3) Zero gas and moneywastage – cost of gas production proportional to usage.
4) Absence of orderprocessing for refills – lower admin/logistics costs.
5) Total safety – nolarge amounts of gas stored onsite.
6) No storage andtransportation cost – low environmental footprint.
In summary, most companiescan improve their nitrogen sourcing through self-producing this valuable gas. So,let us now understand the available onsite gas generation technologiespreferred in industrial applications:
- Membrane technology;and
- Pressure swingadsorption (PSA type).
Let us explore in briefabout the working principle of nitrogen generation technologies.
Membrane technology and how it works
Membrane nitrogengenerators are based on a simple working principle. The main part of a membranegenerator is the membrane module (+-10cm in diameter), filled with small,hollow polymer fibres.
The dry and cleancompressed air enters and due to the structure of these fibres, differentcomponents of the air flow to outside of the fibre. This process is calledpermeation.
During this process, waterand oxygen exit through the membrane sides of the fibres. In the end, onlynitrogen remains. This is possible since different molecules permeate atdifferent speeds. H2O will permeate very quickly; oxygen takes a little longer.
Because of the permeationthrough the fibre wall, an overpressure would occur inside the membranehousing. The fibres would clog, and the permeation efficiency would besignificantly lowered. To prevent that from happening, there is an opening inthe housing, the permeate vent, where these ‘exhaust’ gases can escape.
It is very important forthe intake air to be clean and dry before it enters the membrane. If this isnot the case, the shallow fibres will quickly clog. To prevent this fromhappening, correct air treatment of the feed air must be installed.
In some cases, the neededfilters and dryers will already be built into the generator itself. This wouldmean that, at times, no additional filters should be installed between thecompressor and generator.
The fibres of the membranecan handle water vapour without many problems. It is, however, very importantthat the air be devoid of water, since this will have a detrimental impact onthe membrane.
Therefore, a good waterseparation solution should be in place upstream from the generator. Taking careof the intake air of the generator will protect the membrane and ensure a longlifetime.
Pressure swing adsorption (PSA) and how it works
Adsorption is the processin which atoms, ions, or molecules from a substance (compressed air) adhere tosurface of an adsorbent. PSA nitrogen generator isolates nitrogen, and theother gases in the compressed air stream (oxygen, CO2 and watervapour) are adsorbed, leaving behind essentially pure nitrogen. PSA nitrogengenerator technology is a simple, reliable, and cost-effective approach tonitrogen generation that enables continuous, high-capacity nitrogen flow at thedesired level of purity.
PSA traps oxygen from thecompressed air stream when molecules bind themselves to a carbon molecularsieve. This happens in two separate pressure vessels (tower A and tower B),each filled with a carbon molecular sieve that switch between a separationprocess and a regeneration process.
Clean and dry compressedair enters tower A. Since oxygen molecules are smaller than nitrogen molecules,they pass through the pores of the sieve. Nitrogen molecules cannot fit throughthe pores, so they bypass the sieve resulting in nitrogen of desired purity. Thisphase is called the adsorption or separation phase.
Most of the nitrogenproduced in tower A exits the system, ready for direct use or storage. Next, asmall portion of the generated nitrogen is made to flow into tower B in theopposite direction. This flow pushes out the oxygen that was captured in theprevious adsorption phase of tower B.
By releasing the pressurein tower B, the carbon molecular sieves lose their ability to hold the oxygenmolecules, which detach from the sieves and get carried away by the smallnitrogen flow coming from tower A. This ‘cleaning’ process makes room for newoxygen molecules to attach to the sieves in the next adsorption phase.
Summary
Being an inert gas, nitrogenfinds applications in a wide range of uses and many different industriesincluding oil & gas, marine, electronics, food & beverage packaging,laboratories, fire prevention, pharmaceutical, marine, and general industry. Thisis because one of the most unique properties of this colourless and odourlessgas is its low reactivity, which benefits many processes.
In conclusion, nitrogengenerators are now considered essential equipment in various sectors of theeconomy due to their provision of environmental sustainability,cost-effectiveness, improved production efficiency, and purity control. Withthe market projected to soar to US$16.54-billion by 2033, particularly in theAsia-Pacific region, their transformative impact is undeniable. Thesegenerators pave the way for a more productive, sustainable, and competitivefuture in manufacturing and other industries by revolutionizing industrialprocesses.
Atlas Copco's nitrogengenerators offer a sustainable, reliable, and cost-effective solution,enhancing operational efficiency and environmental stewardship. Nitrogengenerators are used by different sectors like Oil & Gas, Glass Industry,Plastic injection moulding, Food and Beverage, Pharmaceutical and Chemicalapplications, etc. The good news about generating on-site nitrogen is that ifyou already have an air compressor, you are halfway there. All you need is aconnected nitrogen generator unit to generate your own nitrogen in-house.
Atlas Copco India offers awide range of reliable, high-purity, on-site nitrogen gas generator equipment.
Link: https://www.atlascopco.com/en-in/compressors/products/nitrogen-generators