Optimus Sinter is a digital tool to improve iron ore sintering plants operations.
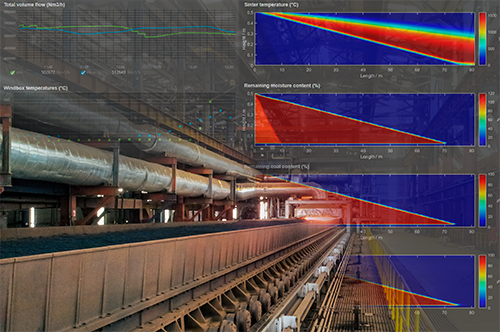
MetsoOutotec is launching Optimus Sinter, a digital optimizer for iron ore sinteringplants. The new tool facilitates improved sinter plant process performance andstability by holistically optimizing the overall sintering processes.
OptimusSinter is one of Metso Outotec’s leading-edge digital solutions to ensure theoptimal operation and maintenance of iron ore sintering plants. A sophisticatedthermodynamic model forms the core of Metso Outotec’s Optimus Sinter; itcalculates the process conditions in the sinter bed, which cannot be measuredwith sensors due to the high temperatures, and offers advanced insights intothe sinter plant operations.
“WithOptimus Sinter, operators can manage the plants better by leveraging theadvanced insights this digital tool offers. Optimus Sinter also offersreal-time operating advice with respect to different operating plant targets,” sharesAndreas Meier-Hedde, Senior Product Manager for Sintering technology at MetsoOutotec.
Backed byMetso Outotec’s decades of experience and process know-how in sintering,Optimus Sinter offers benefits such as increased gross production, improvedelectrical energy consumption and reduced solid fuel consumption. Based onprocess measurement and actual raw material data as well as the proprietaryprocess model, Optimus Sinter provides:
- Online, real-time process calculations.
- Monitoring of relevant process parameters and KPIs (energy consumption and CO2 footprint).
- Visualization of chemical and physical processes and temperatures in the sinter bed.
- Online optimization of feed material mix.
- Real-time forecast of product quality (sinter strength, Fe/Fe2+ content, basicity).
- Improved burn-through calculation.